What is a Value Stream Anyway?
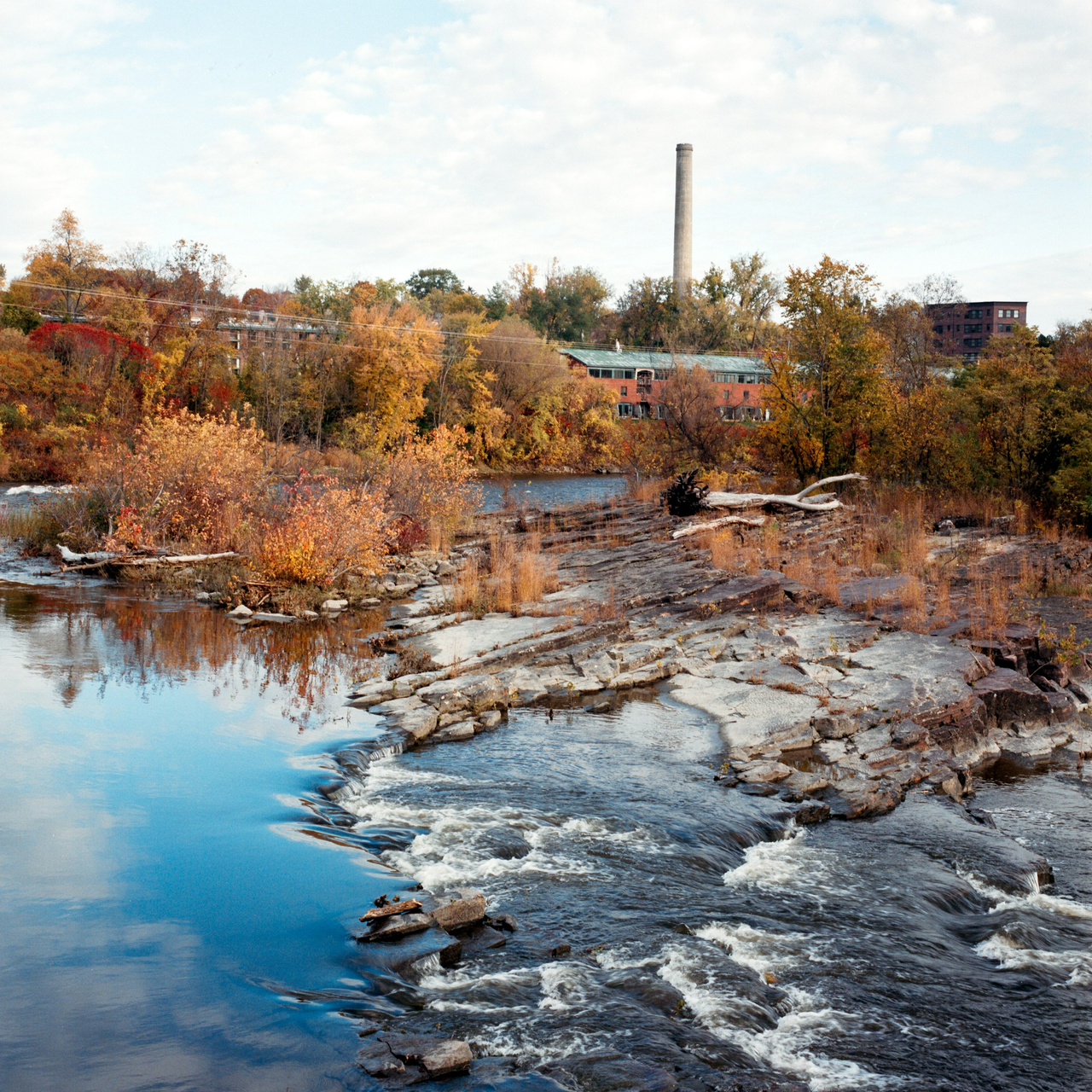
It’s common to hear a term like this and dismiss it as empty business-speak: “We’re going to leverage cross-functional synergies in our value chain to drive growth for stakeholders!”…
But, please trust me, it’s more than that.
Whether you recognize it or not, if you have ever tried to map out the steps of a manufacturing system to understand what’s happening, you have likely used parts of the Value Stream Mapping toolkit. It’s how you establish the base case for your system and create a shared understanding for continuous improvement.
Parts of Value Stream Mapping are intuitive - “What steps turn inputs into outputs and how long do they take?” Others require more thought and study - “What’s the difference between balancing and leveling?” or, “What is the impact of inventory on my throughput time?” Regardless it’s worth understanding how and why to map out your manufacturing system as a Value Stream to help drive continuous improvement.
If you want to dive deep into the topic, there is a mountain of information available both in print and online about Value Stream Mapping as well as the separate, but related Theory of Constraints. I highly recommend both “Learning to See”, and “The Goal” as jumping-off points.
For the tl;dr version - Value Stream Mapping is a way to visualize your manufacturing system as a network of nodes and relationships that turn raw materials into finished goods for customers.
- Value: what your customer is willing to pay for
- Stream: how that value flows to your customer
- Map: a structured, visual representation of the system
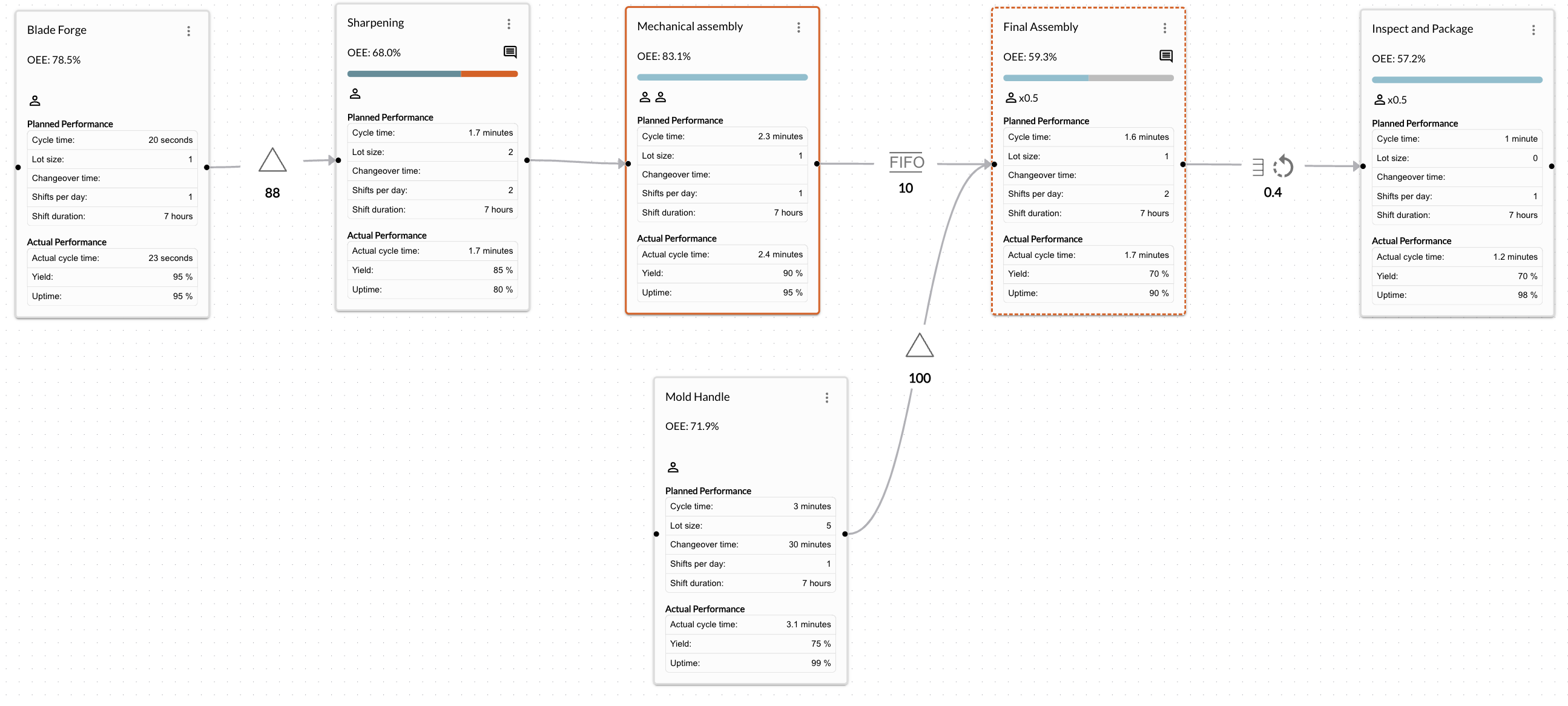
A simple value stream map built in threaded showing the manufacturing system to build a pocketknife
With a small amount of data in the map - things like customer demand, cycle times, changeover frequency, and inventory levels between nodes - you can see how efficiently value will flow to your customer, whether or not your can satisfy customer demand, and where you have a bottleneck or constraint. Essentially, you are looking for logjams that could constrain flow - things like yield loss, machine availability, or operations taking longer than planned, as well as areas where inventory is building up. This first pass is deemed your “current state”, and with it you can understand where to deploy resources to mitigate those constraints to create a “future state” where value will flow more efficiently, increasing profitability. Wash, rinse and repeat for continuous improvement.
#Why does it matter?
It’s no secret, but manufacturing is hard! Deceptively so in fact. Each part of a manufacturing system is often simple - buy a part, put it on a shelf, cut/form/mold it, attach it to 3 other parts, etc. But combined into a dynamic system tasked with continuously improving profitability - that is, manufacturing - it quickly becomes something that a person can’t keep in their head. Let alone a full team of people working in different functions. As well, when launching a new product, it’s critically not just the product that needs to be designed and validated, but rather the complete manufacturing system to build it.
Enter the benefits of a Value Stream Map.
#Alignment on a shared understanding of the system.
If you don’t know where you’re going, any road will take you there. -Cheshire Cat.
Continuous improvement sounds great, but it’s impossible to do without a starting point and an objective. This is even more true with a cross-functional team. If the team isn’t clear on the nature and status of the system, and there aren’t obvious system-level metrics that describe performance and improvement, it’s nearly impossible for them to do.
The Value Stream Map creates that shared understanding. It’s approachable, helps everyone to see the big picture, and has clear metrics for performance and improvement - takt time, throughput time, processing time, yield, etc.
#See your constraints - so you can fix the right things
An hour saved at a non-bottleneck is a mirage. - Eliyahu M. Goldratt
It’s really easy to be busy in a factory without being productive. How is this possible? Well, there are a million issues screaming for attention, but only a handful of them are rate-limiting constraints/bottlenecks. If you address those constraints, value will flow more readily. If you fix things that don’t constrain the system… nothing happens.
A Value Stream Map helps you clearly identify your constraints so you can focus efforts and resources accordingly. It also makes this visible to the full team - people generally want to do the right thing and work on things that will be impactful for the system at large, but if they don’t know what those things are, they can’t do so.
#Collaboration
A company could put a top man at every position and be swallowed by a competitor with people only half as good, but who are working together. - W. Edwards Deming.
This isn’t a secret, but the way you get things done in manufacturing is by working together. But, what exactly are you collaborating on? Mapping out the Value Stream gives the team a shared understanding of what they are working on and why to help avoid just working on changing issues of the day. Once you’ve mapped the system and can see the constraints, you can kick off activities to change and improve the Value Stream together with a shared focus across the team. This is sometimes formalized as a “Kaizen Event” or “Rapid Improvement Workshop”. Essentially getting your team to work together to drive improvement, knowing that the output will be impactful to the system as a whole.
#How Threaded can Help
At Threaded, the core of our product is a collaborative, web-based Value Stream Map. While the benefits above are all real no matter how you map your value stream, we’re helping you dial them up and making them more accessible.
#With Threaded, you can
Map your value stream.
- Keep things visible in an online platform where you can map your current state, your future state, and what it takes to get there.
Get actionable Insights.
- Our insights engine finds your constraints, so you can make sure you focus on the right things to drive improvement.
Collaborate with your team.
- Probably most importantly - invite your team to help map, comment, and solve problems in real time. Working together you’ll get better results, faster.
Continuously Improve.
- Kick off actions and provide visibility as you drive them to completion with your team.
Dive in anywhere
- Collaborate wherever you are from the office to the factory floor.
Sign up here, start mapping, and invite your team today! It’s free for 3 collaborators on 6 Value Streams, and we can’t wait for you to use it to start improving.