Manufacturing is Harder Than it Needs to Be
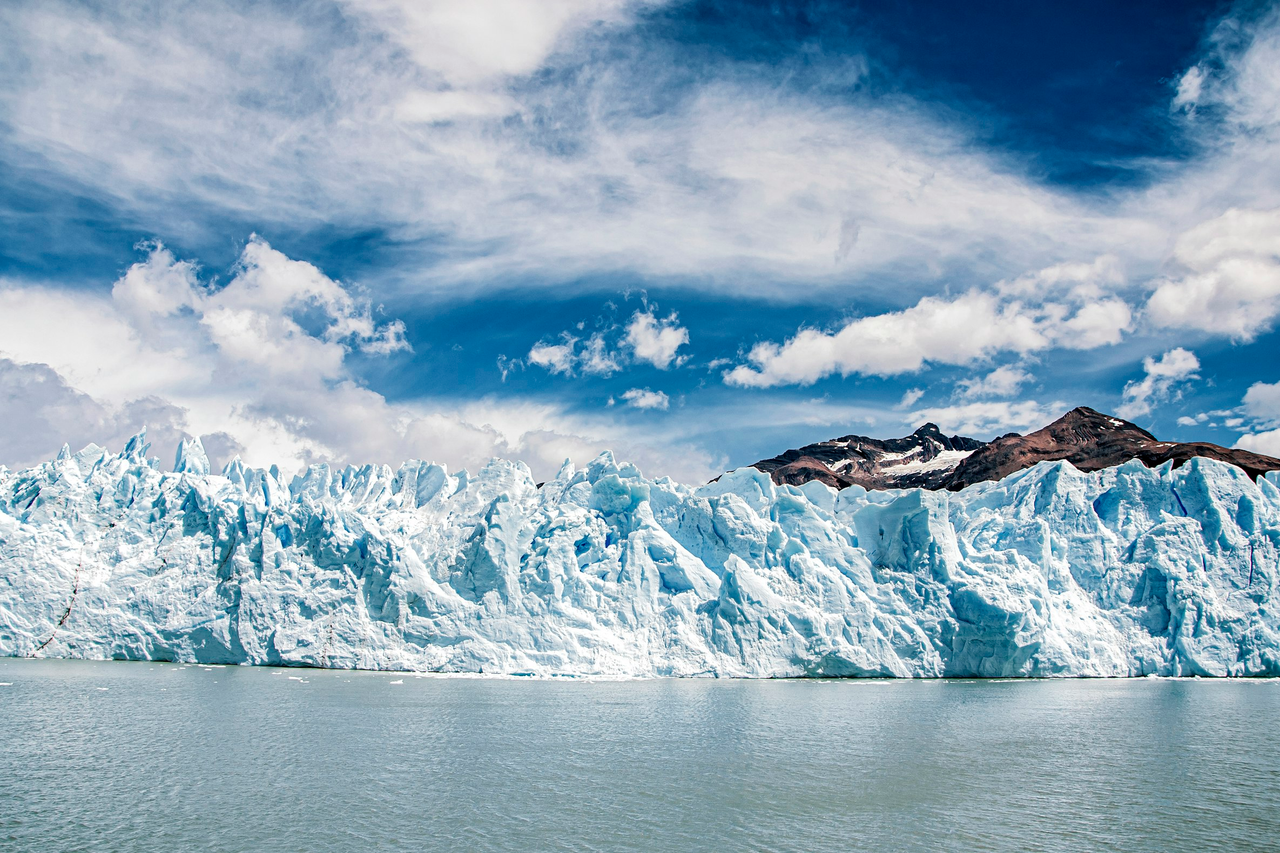
When I was first studying manufacturing a professor asked a simple question: “What gets manufactured?” After the first few responses – cars, airplanes, machinery – it became clear these were not the desired answer. As we dug deeper, shouting out whatever we could see – backpacks, desks, carpet, projectors, pens, etc., the answer became clear:
Everything.
At least everything tangible. This is intuitively obvious, but is something that I and everyone else had simply taken for granted. Almost any physical product goes through a system that turns raw materials into products that people are willing to buy. In other words, Manufacturing.
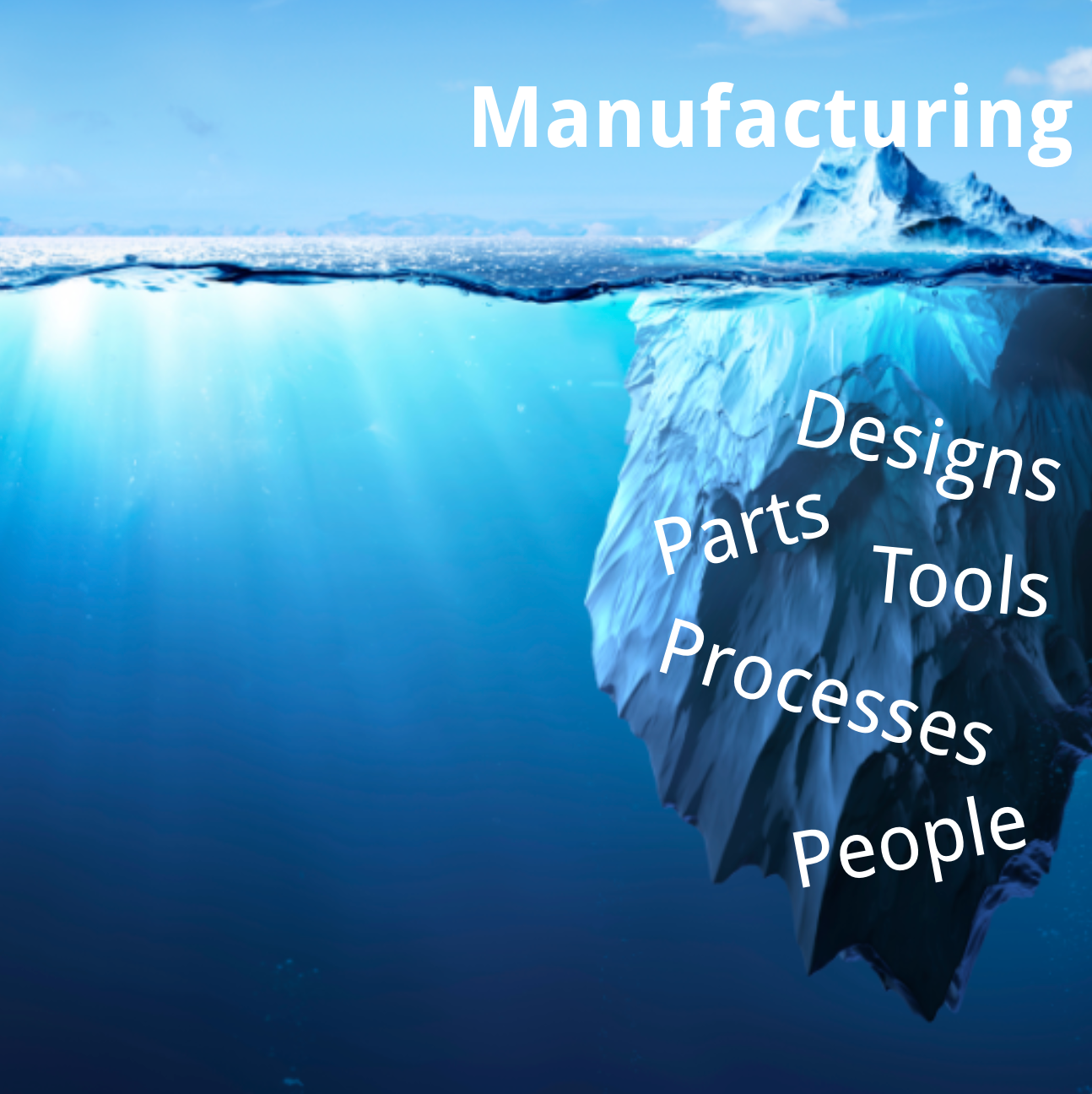
The critical system of designs, parts, tools, processes, and people is there but out of view.
#Manufacturing: An iceberg of complexity
Just like my classmates and me, consumers generally take manufacturing for granted. We focus intensely on cool new features and the price to obtain them, but almost never on how they get built. We all know manufacturing exists, but it’s like an iceberg — the critical system of designs, parts, tools, processes, and people is there but out of view. It’s difficult to really comprehend, and it isn’t the top concern when making a purchasing decision. While not a problem per-se, it does mean that this $2.3T1 component of our economy is often only superficially understood.
This lack of comprehension means that manufacturing is simultaneously under-appreciated and feared. It’s often seen as either a trivial matter to be dealt with after product testing, or as too complex and difficult to take on. Take the following common statements:
The prototype is amazing, now we just have to manufacture it!
and
Manufacturing isn’t our core competency, it will be easier to just find a contract manufacturer.
Both statements are often spoken by someone headed straight into an iceberg.
A great example of the first statement are hardware projects on Kickstarter. 60% of them fail2, and over 75% of failure modes3 can be attributed to challenges with manufacturing. It’s not that people aren’t trying or didn’t come up with a great product, just that they all too often underestimate the challenge and complexity.
The second statement could be it’s own post, but I’ll let you in on a little secret – manufacturing your product isn’t the core competency of any contract manufacturer either. When they need new equipment, they will find a way to have you foot the bill. When problems inevitably arise, you will have to do the work to make them successful. If they fail, you fail, and while manufacturing success means increased profits for them, success means survival to you. In the process you’ll do all the hard work to make manufacturing a core competency — but for them. This may still be the right strategy, but the point is that it’s never as easy as simply paying someone else to do the hard part.
#Success in Manufacturing is Hard
This is a natural conclusion, but is often difficult to see. It’s the bottom of the iceberg, and when problems do arise most people try to blame external factors. Admitting manufacturing is difficult and that you aren’t an absolute expert doesn’t usually inspire confidence. That said, Elon recently went out of his way to drive home how difficult manufacturing really is. When discussing the recently-launched Cybertruck, he shared that “It’s trivial really to churn out prototypes, and it is extremely difficult to build a factory… Manufacturing is somewhere between 100 and 1000 times harder than making a prototype… I really can’t emphasize enough how hard production is compared to design4”. The next logical question though, is given all of the progress that’s been made since the beginning of the industrial revolution, and all of the advances in technology — why is it still this hard?
I really can’t emphasize enough how hard production is compared to design.
- Elon Musk
While at first glance it seems like a one-off function that could be easily optimized with technology, it’s really a highly complex, interconnected system that must perpetually operate and continuously improve. It can’t be dealt with as a silo, and is never “done”. Unfortunately, humans just aren’t good at comprehending complex systems like this without an assistive framework, and where today’s tools primarily optimize for discrete functions over the system, it becomes much more difficult than it needs to be. Finally, contrary to the perception that factories are mostly automated, using robots (and soon AI) to crank out whatever widget you want at the push of a button, in reality they are reliant on and managed by people. Those people are hyper-critical in developing and operating the system profitably, but unless they have the right framework to understand the system, they soon start flying blind.
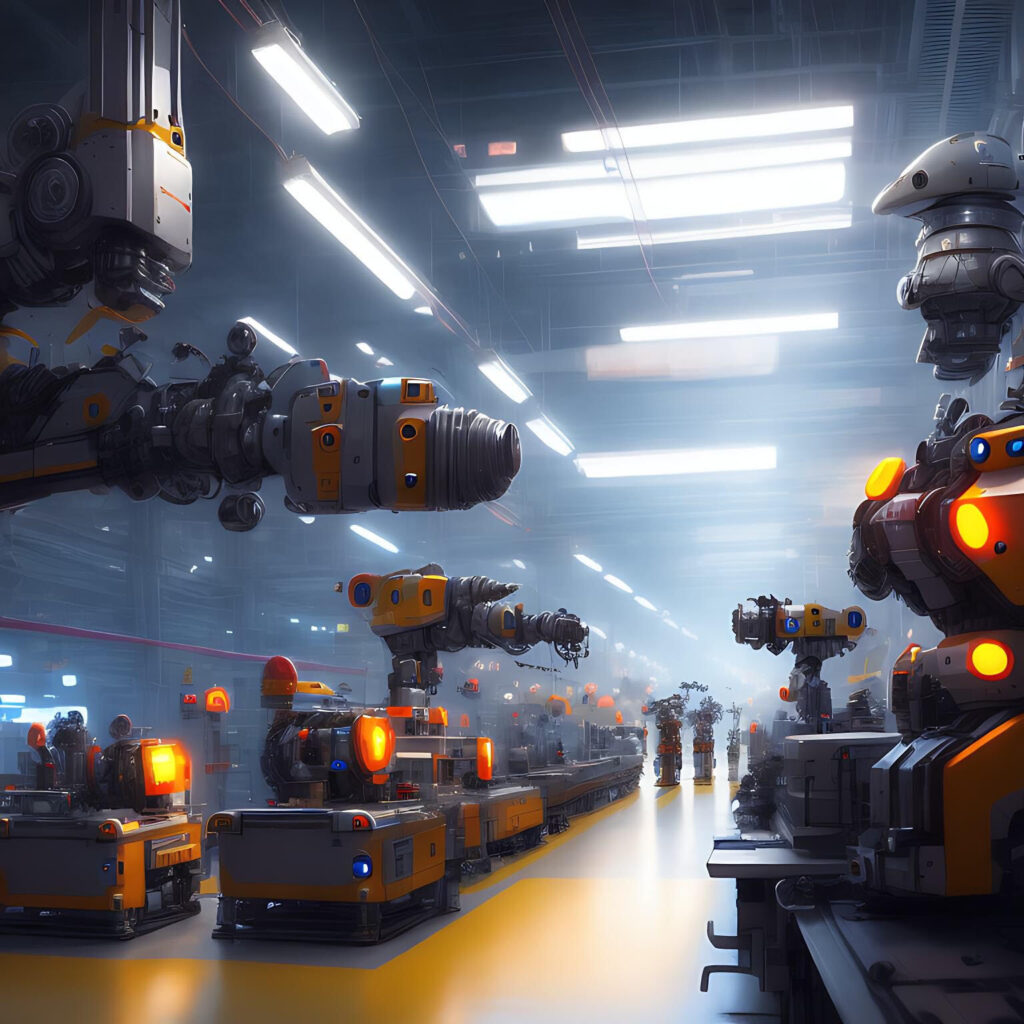
AI concept of a modern factory. It has a lot of advanced automation but misses everything else... and doesn't make much sense.
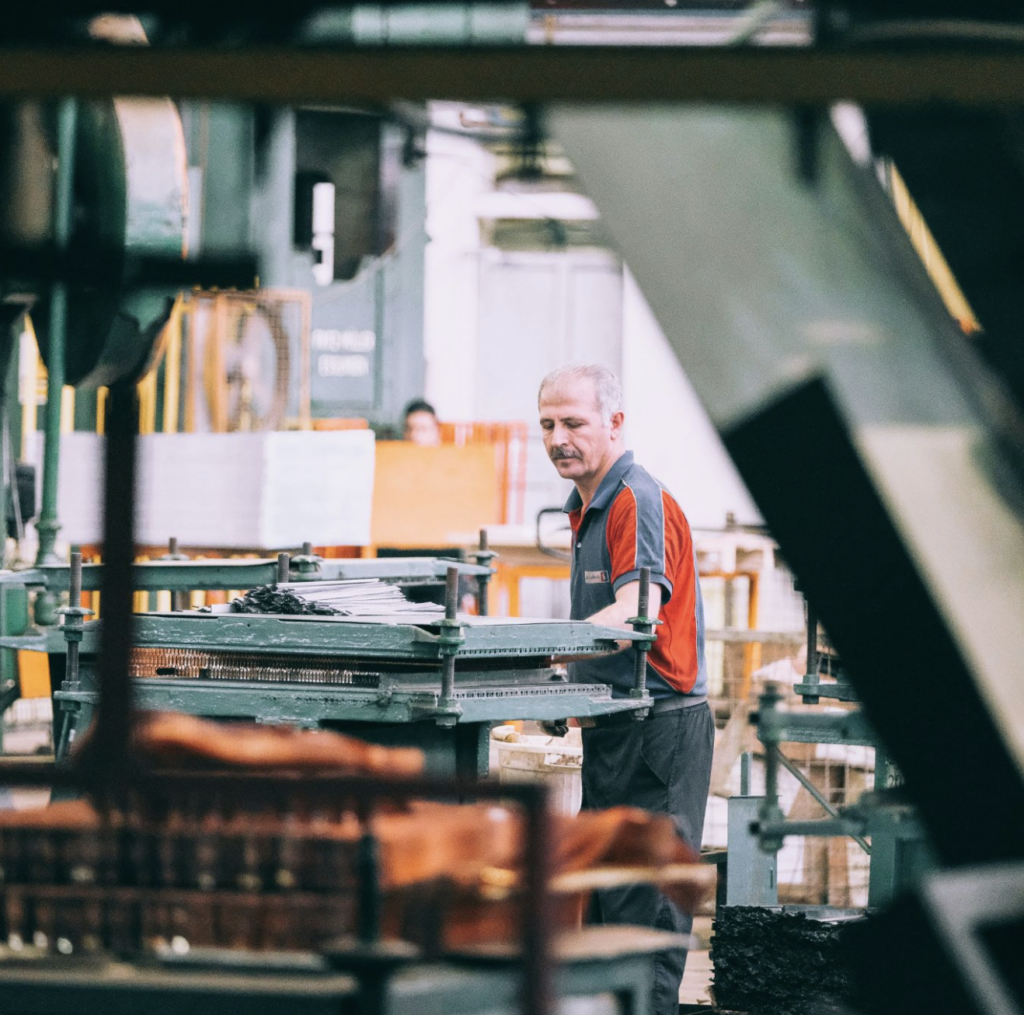
Actual Manufacturing – Tools, Parts, Processes, and People. Not fancy, but how value is created.
#Strategies for dealing with this complexity
The next question then, is given this complexity, how do we drive success in manufacturing? After all – I can buy all kinds of products today, so it can’t be that hard. Right? After launching products into factories all over the world, I can say emphatically that yes, it is that hard. However, it’s not impossible, and I’ve also found that the most critical driver of manufacturing success is a team of people, working together, that understand what will happen to the system if they make a change – be it a design, a tool, a process, or anything else. This happens in one of three ways:
- Have a single person with a near-perfect understanding of the entire system lead the team.
- Never change once the system is “working”.
- Clearly communicate who and what may be impacted by a change, and collaborate accordingly.
#Strategy 1 – The Omniscient Leader
This works in a simple operation, but quickly becomes impossible. You just can’t keep everything in a single person’s head. As a personal example, early in my career I was a process engineer at a factory building diesel engines. We tested engines mid-build, with multiple test cells to account for various engine models. The cells were not universal, and this test would often become a bottleneck and stop the line depending on the model mix being built. I realized that by enabling one of the cells to test more models, I could meaningfully increase throughput efficiency and eliminate the bottleneck. I did exactly that, noticing that a test probe came very close to the new model’s oil filter, but it didn’t cause any problem with the test so I let it slide.
Everything was great for a few days, until I was confronted by two very angry colleagues from the paint shop downstream. They had a huge pileup of defects that was just getting larger, and no idea where it was coming from. They were walking upstream, and once they found me, you guessed it – we realized the defect was being caused by a minor scratch from that probe on the oil filter.
We can argue whether a minor bump in the paint of a serviced component buried under the hood of a tractor should really be classified as a quality defect. However, the point is that I made a change and thought everything was fine, but caused a massive headache for downstream colleagues in the same system. It was a mess, but I had no way of knowing any possible effects of this change, nor did the people around me. The downstream team had no way of knowing what changed and was causing them problems, and so it caused an outsized system disruption.
#Strategy 2 – “Just Stop Changing!”
This sounds great in principle, but it’s simply not possible. Modern customers require differentiated goods that fit their needs and have ever-improving features and costs. This drives change into the system, as does competition and the never-ending requirements for increased productivity, efficiency, and reduced costs. This is only possible with change, and if you don’t do it, your competitor will.
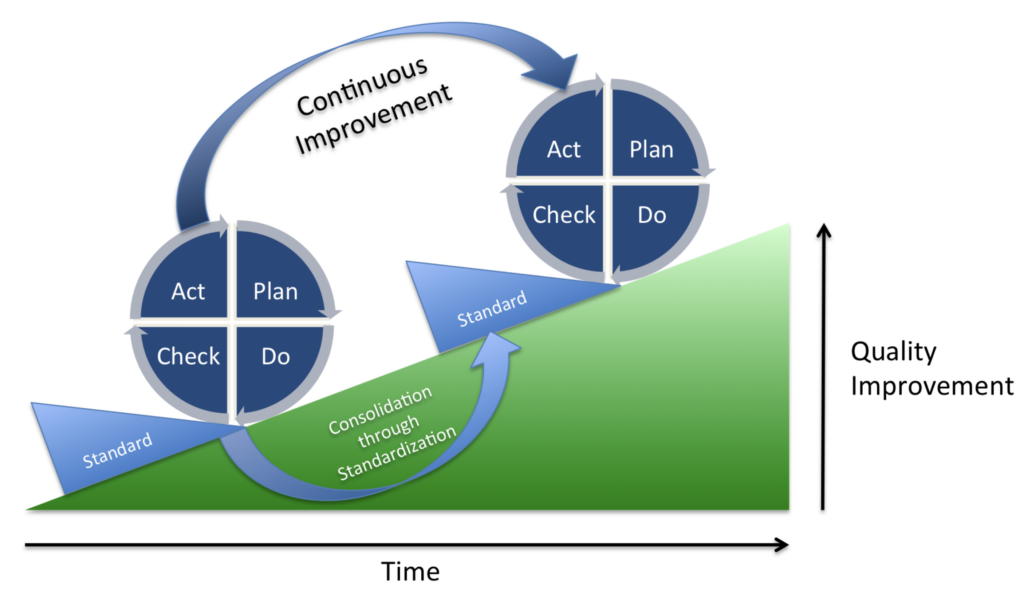
From Wikipedia: Continuous improvement through the “Plan Do Check Act” (PDCA[^5]) method in manufacturing. This process and those like it are necessary to stay competitive, and the “Do” means “Change” – you can’t stay stagnant.
#Strategy 3 – Communicate and Collaborate
Make sure that everyone in the system knows what’s going on, so they can work together to effectively process change. In practice, this is the only viable strategy, and I generally end up here after starting as (or with) an omniscient leader. However, it can really only be done manually. Yes some siloed data can be automatically collected and communicated, but stitching together a view of the complete system requires a huge amount of manual overhead. This is fraught with errors, which means the manually managed data has to also be manually reviewed – regularly and at great expense.
During development, this translates to regular – often daily – meetings with the full team to discuss where you are, where you are going, and who needs to do what, with whom, by when to get there. All while responding to unplanned issues that invariably arise.
In operation, it means a regular rollup – sometimes twice daily – from the manufacturing cell, up to the group, up to the factory level, and then back down again. It works, but requires a ton of overhead, and a mountain of tedious, error-prone, manual work in spreadsheets to share information. Even so, surprises, diving catches, and disaster-management are common as issues get lost until it is too late to do anything but fight the fire. As well, this model naturally drives chain of command communication up and down the organization, which is generally the slowest and least-effective way to actually solve a problem.
#We launched Threaded to address this problem
Manufacturing is harder than it needs to be because it requires people to manually manage the complexity of their manufacturing system. This is inherently fraught with errors and distracts from improving products and processes for customers. Our starting point is to build the framework around which manufacturing development and operating teams can collaborate, and our initial product will help them do so for Product Launch and Continuous Improvement.
We’re still in Beta, but if you’re interested in what we’re building, join the waitlist and we’ll get you into our next batch. As well, this is only the start. Would love to hear if you have other challenges with your manufacturing system that we may be able to help with!
Until then, keep building awesome products! It’s hard, but we’re all grateful for it.
-Braden
#Footnotes
Build with Threaded
The Collaborative Build Book with a data-driven Value Stream Map.
Built by builders, for builders.