'Let 'Er Roll!!!' A Manufacturing Case Study
While there aren’t any good manufacturing movies, this clip from “I Love Lucy” is pretty solid.
There’s no big story arc, eureka moment, or inspiring success, but there are bunch of practical takeaways. Take 3 minutes, get a few laughs, and lets dig in!
#Manufacturing is a system, and systems are hard
Chocolates are simple, but manufacturing gets complex quick. We only see Lucy in the wrapping station (the full episode also shows a fiasco in dipping), but here’s a hypothetical value stream to illustrate the system.
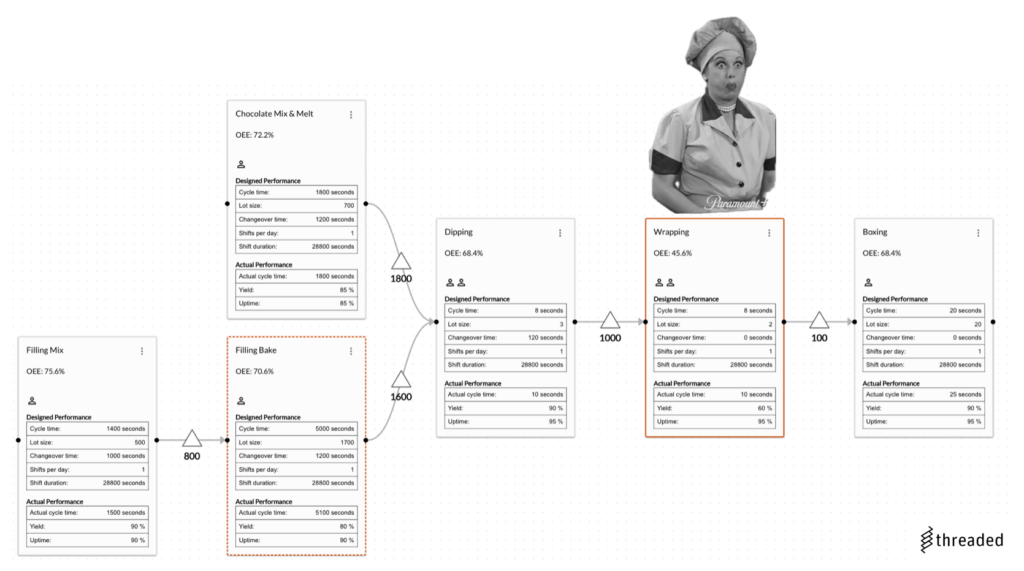
A hypothetical value stream for making chocolates in I Love Lucy, with the primary constraint being wrapping, and the secondary constraint being baking the filling.
She and Ethel are downstream chocolates being made, and can’t keep up with the upstream rate - they’re a bottleneck. Rather than limit the output of the system, they try to find ways to go faster - because if they don’t… “YOU’RE FIRED!” and everything explodes.
#A combination of simple things is not simple
Each step is simple, and each is made up of a collection of other simple things - ingredients, instructions, tools, etc. They also have simple rules for operation - batched mixing, backing, and melting, and a connected assembly line for dipping, wrapping, and boxing.
Humans can intuitively understand simple, static components - “Well, this is easy!”. What we can’t easily grasp is how they work together in a continuous, dynamic system. This isn’t just a manufacturing thing - fluid mechanics, Conway’s Game of Life, and the butterfly effect are all examples of how simple things quickly become complex.
If we’re not careful, we mistakenly attribute component simplicity to the system at large, and don’t realize we’ve got a problem until it’s too late. “Ethel… I think we’re fighting a losing game!”
#Dealing with the complexity
First recognize that manufacturing is a complex system, and that you can’t keep it all in your head. To understand it, a value stream map is a good place to start. Include objectives for rate, quality, and cost, and do so collaboratively. A special aspect of manufacturing systems is that they always includes people, meaning the more affected people you can include in the mapping process, the more likely you are to understand exactly what’s happening.
#What else can we learn from Lucy and Ethel?
We have to know what we’re building
In the candy factory this is candy, right? Kind of. “Candy” needs to be more clearly defined as a set of design specifications that can be shared and referenced throughout the system.
Lucy and Ethel are only told “…take each piece of candy, and wrap it in one of these papers”, but what does wrapped mean? Is there a specific shape? We see chocolates coming loose immediately, but can we say that’s wrong?
#Replenishment - 99% of parts isn’t enough
Candy comes from upstream on the conveyor belt, but what about the papers? There is no path for replenishment - just a stack at the bench - and they were never told how to get more. Even if Lucy and Ethel could keep up, they were bound to fail as soon as those papers ran out.
This situation is unfortunately common - lots of focus on the “chocolates”, but the cheap papers are ignored until it’s too late. Critical manufacturing lines can easily go hard down for something as simple as a missing bolt, and it’s maddening.
The solution? Ensure you have a clear path for replenishment for everything - especially the small stuff that people won’t be monitoring closely. You can usually deploy a simple, replicable kanban with minimal overhead.
#Focus on consistency - not just speed
In the wrapping department the only tool is the conveyor belt, and it has one purpose: speed. They get speed - “Turn it up a little!” but that just causes problems faster.
Watching Lucy and Ethel work, they each wrap differently, have no idea if they are doing things wrong or right, and candies are constantly coming undone. Standard Work would be hugely beneficial, or a fixture to help them consistently hit a spec for the wrapper (assuming one exists).
The adage from the SEALs rings true here - Slow is smooth, smooth is fast. Focus on consistency first, and as you nail that speed will naturally come.
#Wrapping up
There are probably dozens more lessons we could pull from these 3 minutes, but the most important is that while manufacturing is often a combination of simple things, it’s far from simple itself. If Lucy and Ethel (and their employer) had recognized their candy factory was a complex system - and managed as such - they would be able to find and fix the core of their issues, and avoid the chocolate pile-up.
At Threaded we’re building the platform to help teams collaboratively develop and launch their manufacturing systems. We’re just getting started, but if you’d like to learn more, sign up for a demo – we’d love to chat!